Unlocking Electic Vehnicle Battery Potential with High-Performance Tool Steel
Electric vehicle (EV) batteries are the core component of electric vehicles, responsible for storing energy and powering the vehicle efficiently. They play a critical role in enabling longer driving ranges, making them essential for the growth of sustainable, zero-emission transportation. EV batteries are composed of multiple parts, each with specific tasks and requirements. The quality and performance of these components are critical to the overall effectiveness of the battery. High-performance polymers for battery parts are one of the options to extend driving ranges due to their greatest feature, such as lightweight.
One key material used in the production of EV battery plastic components is tool steel. Tool steel solutions are specifically engineered to meet the rigorous demands of EV battery production. Its key properties—high hardness, excellent wear and corrosion resistance—allow it to withstand the harsh operating conditions when manufacturing the battery parts, contributing to longer service life.
When processing plastics used in EV batteries that consist of Halogen-Free Flame Retardants (HFFR), mica, and a high amount of glass fibres, it is crucial to select the right grade of tool steel, such as corrosion-resistant steel with the necessary hardness. Tool steel with a uniform microstructure ensures texturing or smooth surface requirements, significantly improving the performance of battery components.
Challenges | Characteristics | Tool Steel Solution |
---|---|---|
Halogen-Free Flame Retardants | Corrosion resistance | Stainless steel grade |
Mica, glass fibre | Wear resistance | High hardness |
Texturing, smooth surface | Surface requirement | uniform microstructure |
By utilising these advanced tool steel solutions, manufacturers can achieve production of high quality of EV battery components, ultimately enhancing the efficiency and longevity of electric vehicles.
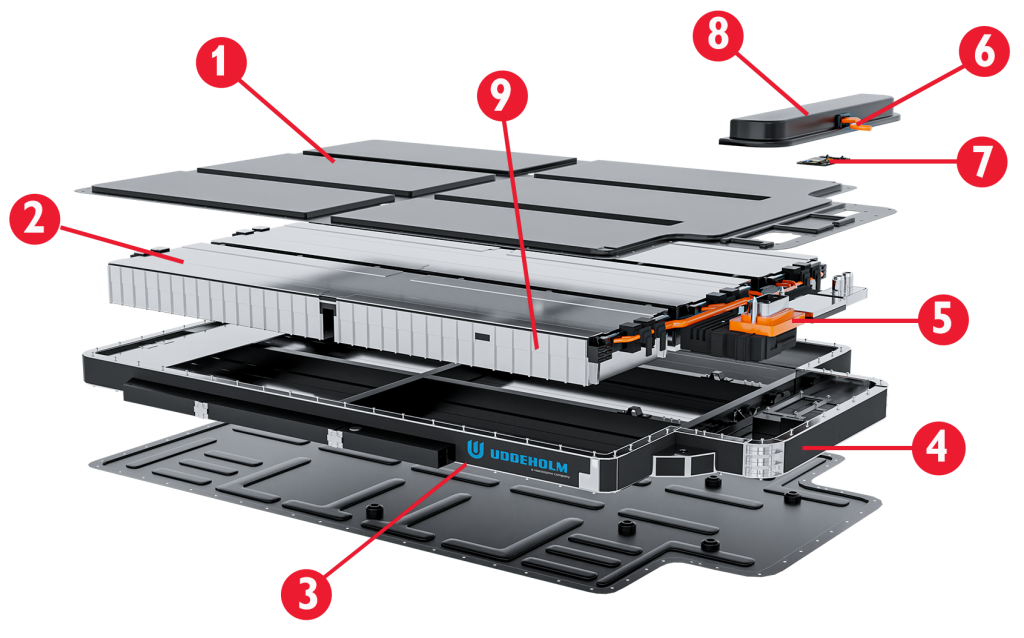
Here are ASSAB’s solutions for the different parts of the EV battery:
Parts | Required Properties | Short to medium die life (~40 HRc) | Long die life (~58 HRC) | Longest die life (≥60 HRC) |
---|---|---|---|---|
1. Battery housing/Cover | Corrosion resistance High strength (glass fibre) | Mirrax 40 | Corrax (~50HRC), Stavax ESR (~52HRC), Mirrax ESR(~52HRC), Tyrax ESR (~58HRC) | Elmax SuperClean (~60HRC), Vanax SuperClean (60HRC) |
2. Cell module | Corrosion resistance High strength (glass fibre) | Mirrax 40 | Corrax (~50HRC), Stavax ESR (~52HRC), Mirrax ESR(~52HRC), Tyrax ESR (~58HRC) | Elmax SuperClean (~60HRC), Vanax SuperClean (60HRC) |
3. Cooling System | Corrosion resistance | Mirrax 40 | Corrax (~50HRC), Stavax ESR (~52HRC), Mirrax ESR(~52HRC), Tyrax ESR (~58HRC) | Elmax SuperClean (~60HRC), Vanax SuperClean (60HRC) |
4. Battery Frame Tray | Corrosion resistance High strength (glass fibre) | Mirrax 40 | Corrax (~50HRC) Stavax ESR (~52HRC) Mirrax ESR(~52HRC) Tyrax ESR (~58HRC) | Elmax SuperClean (~60HRC), Vanax SuperClean (60HRC) |
5. Module Connector | Corrosion resistance High strength (glass fibre) | Mirrax 40 | Corrax (~50HRC), Stavax ESR (~52HRC), Mirrax ESR(~52HRC), Tyrax ESR (~58HRC) | Elmax SuperClean (~60HRC), Vanax SuperClean (60HRC) |
6. EV Connector | Corrosion resistance | Mirrax 40 | Corrax (~50HRC), Stavax ESR (~52HRC), Mirrax ESR(~52HRC), Tyrax ESR (~58HRC) | Elmax SuperClean (~60HRC), Vanax SuperClean (60HRC) |
7. Battery management controller * | Wear resistance High strength (glass fibre) | ASSAB 718 HH, Nimax | Vidar 1 ESR (~50HRC), 8407 Supreme (~50HRC), Unimax (~58HRC) | Caldie (~61 HRC) Vanadis 4 Extra (~64HRC) |
8. Battery junction box * | Wear resistance High strength (glass fibre) | ASSAB 718 HH, Nimax | Vidar 1 ESR (~50HRC), 8407 Supreme (~50HRC), Unimax (~58HRC) | Caldie (~61 HRC) Vanadis 4 Extra (~64HRC) |
9. Housing tray * | Wear resistance High strength (glass fibre) | ASSAB 718 HH, Nimax | Vidar 1 ESR (~50HRC), 8407 Supreme (~50HRC), Unimax (~58HRC) | Caldie (~61 HRC) Vanadis 4 Extra (~64HRC) |